The basic composition of the bearing code The code of the rolling bearing The basic composition of the rolling bearing code The rolling bearing code – prefix The rolling bearing code – the suffix – the pre-code The pre-code R is placed directly before the basic code of the bearing, and the other codes are separated from the basic code by a small dot open. GS.——Thrust cylindrical roller bearing race. Example: GS.81112. K.——Assembly of rolling element and cage. Example: Thrust cylindrical roller and cage assembly K.81108 R – Bearings without separable inner or outer rings. Example: RNU207——NU207 bearing without inner ring. WS——Thrust cylindrical roller bearing shaft washer. Example: WS.81112. ——Internal Design——Outline Dimensions and Deformation Design——Seal——Cage——Tolerance——Gap—Heat Treatment——Special Design——Machine Tool Spindle Bearing——
Low-noise and low-noise bearings – the post code is placed behind the basic code. When there are multiple sets of suffix codes, they should be arranged from left to right in the order of the suffix codes listed in the bearing code table. Some suffix codes are separated from the basic code by a small dot. Subsequent code – internal structure A, B, C, D, E – internal structure change example: angular contact ball bearing 7205C, 7205E, 7205B, C – 15 ° contact angle, E – 25 ° contact angle, B – 40 ° contact horn. Example: Cylindrical roller, spherical roller and thrust spherical roller bearings N309E, 21309 E, 29412E – reinforced design, bearing load capacity is improved. VH——Full complement cylindrical roller bearing with self-locking rollers (the diameter of the compound circle of the roller is different from that of the standard bearing of the same type). Example: NJ2312VH. Subsequent code – bearing dimensions and external structure DA – separable double row angular contact ball bearing with double half inner ring. Example: 3306DA. DZ——Cylindrical outer diameter roller bearing. Example: ST017DZ. K——Bearing with tapered bore, taper 1:12. Example: 2308K. K30- Tapered bore bearing, taper 1:30. Example: 24040 K30 . 2LS——Double row cylindrical roller bearing with double inner ring and dust cover on both sides. Example: NNF5026VC.2LS.V——internal structure change, double inner ring, with dust cover on both sides, full complement double row cylindrical roller bearing. N——A bearing with a stop groove on the outer ring. Example: 6207N. NR——A bearing with a snap groove and a snap ring on the outer ring. Example: 6207 NR. N2———A four-point contact ball bearing with two stop grooves on the outer ring. Example: QJ315N2. S——A bearing with lubricating oil grooves and three lubricating oil holes in the outer ring. Example: 23040S. Spherical roller bearings with bearing outer diameter D ≥ 320mm are not marked with S. X——The overall dimensions meet the requirements of international standards. Example: 32036X
Z••——Technical conditions for special structures. Arranged in descending order from Z11. example:
Z15——Stainless steel bearing (W-N01.3541). ZZ——The roller bearing has two retaining rings that guide the outer ring. Subsequent code – sealing and dustproof RSR – one side of the bearing has a sealing ring. Example: 6207 RSR .2RSR——The bearing has sealing rings on both sides. Example: 6207.2RSR. ZR——The bearing has a dust cover on one side. Example: 6207 ZR .2ZR bearings have shields on both sides. Example: 6207.2ZR ZRN——The bearing has a dust cover on one side and a stop groove on the outer ring on the other side. Example: 6207 ZRN. .2ZRN——The bearing has dust covers on both sides, and a stop groove on the outer ring. Example: 6207.2ZRN. Subsequent code—cage and its material 1 Entity cage. A or B is placed after the cage code, A means that the cage is guided by the outer ring, and B means that the cage is guided by the inner ring. F——Steel solid cage, guided by rolling elements. FA——Steel solid cage, guided by the outer ring. FAS——Steel solid cage, outer ring guide, with lubrication groove. FB——Steel solid cage, guided by the inner ring. FBS——Steel solid cage, inner ring guide, with lubrication groove. FH—Steel solid cage, carburized and quenched. H, H1 – carburizing and quenching cage. FP——steel solid window cage. FPA——Steel solid window cage, guided by the outer ring. FPB——Steel solid window type cage, inner ring guide. FV, FV1——Steel solid window cage, after aging, quenching and tempering treatment. L——Light metal solid cage, guided by rolling elements. LA——Light metal solid cage, guided by the outer ring. LAS——Light metal solid cage, outer ring guide, with lubrication groove. LB—Light metal solid cage, guided by the inner ring. LBS——Light metal solid cage, inner ring guide,
With lubrication groove. LP——Light metal solid window cage. LPA——Light metal solid window cage, guided by the outer ring. LPB——Light metal solid window cage, guided by the inner ring (thrust roller bearings are guided by the shaft). M, M1 – brass solid cage. MA——Brass solid cage, guided by the outer ring. MAS—Brass solid cage, outer ring guided, with lubrication groove. MB—Brass solid cage, guided by the inner ring (thrust spherical roller bearings are guided by the shaft ring). MBS—Brass solid cage, inner ring guide, with lubrication groove. MP – brass solid straight pocket cage. MPA—brass solid straight pocket and cage, outer ring guide. MPB—Brass solid straight pocket cage, inner ring guide. T——Phenolic laminated cloth pipe solid cage, guided by rolling elements. TA——Phenolic laminated cloth tube solid cage, guided by the outer ring. TB——Phenolic laminated cloth tube solid cage, inner ring guide. THB——Phenolic laminated cloth tube pocket type cage, guided by the inner ring. TP – phenolic layer grave cloth tube straight pocket cage. TPA——Phenolic laminated cloth tube straight pocket cage, outer ring guide. TPB——Phenolic laminated cloth tube straight pocket cage, inner ring guide. TN——Engineering plastic injection molded cage, guided by rolling elements, with additional numbers indicating different materials. TNH—engineering plastic self-locking pocket cage. TV—glass fiber reinforced polyamide solid cage, guided by steel balls. TVH—glass fiber reinforced polyamide self-locking pocket-type solid cage, guided by steel balls. TVP—glass fiber reinforced polyamide window-type solid cage, guided by steel balls. TVP2 – glass fiber reinforced polyamide solid cage, roller guide. TVPB—glass fiber reinforced polyamide solid cage, inner ring guide (thrust roller bearing is shaft guide). TVPB1 – glass fiber reinforced polyamide solid window cage, shaft guided (thrust roller bearing). Stamping cage J——steel stamping cage. JN——Deep groove ball bearing riveted cage. The cage change is added after the cage code, or the number inserted in the middle of the cage code, indicating that the cage structure has been changed. These numbers are only used for transition periods, eg: NU 1008M 1 . Subsequent code—no cage bearing V——full complement rolling element bearing. Example: NU 207V. VT – full complement rolling element bearings with spacer balls or rollers. Example: 51120VT. Subsequent code——tolerance grade (dimensional accuracy and rotation accuracy) P0——tolerance grade conforms to the 0th grade stipulated by the international standard ISO, and is omitted in the code, not indicated. P6——The tolerance level conforms to the 6th level stipulated by the international standard ISO. P6X——The tolerance class conforms to the Class 6 tapered roller bearings stipulated by the international standard ISO. P5——The tolerance grade conforms to the 5th grade stipulated by the international standard ISO. P4——The tolerance grade conforms to the 4th grade stipulated by the international standard ISO. P2——Tolerance class conforms to Class 2 specified by the international standard ISO (excluding tapered roller bearings). SP——Dimensional accuracy is equivalent to class 5, and rotational accuracy is equivalent to class 4 (double row cylindrical roller bearings). UP—The dimensional accuracy is equivalent to class 4, and the rotational accuracy is higher than class 4 (double row cylindrical roller bearings). HG——Dimensional accuracy is equivalent to class 4, rotational accuracy is higher than class 4, and lower than class 2 (spindle bearings). Subsequent code—clearance C1—clearance conforms to group 1 stipulated in the standard, and is less than group 2. C2——The clearance conforms to Group 2 specified in the standard, and is less than Group 0. C0——The clearance conforms to the group 0 stipulated in the standard, which is omitted in the code and not indicated. C3——The clearance conforms to the 3 groups stipulated in the standard, and is greater than 0 group. C4——The clearance conforms to the 4 groups stipulated in the standard, and is greater than 3 groups. C5——The clearance conforms to the 5 groups stipulated in the standard, and is greater than 4 groups. When the tolerance grade code and the clearance code need to be expressed at the same time, the combination of the tolerance grade code (not indicated for P0 level) and the clearance group number (not indicated for group 0) is used. Example: P63=P6+C3, which means the tolerance class of the bearing is P6, and there are 3 groups of radial clearance. P52=P5+C2, means bearing tolerance class P5, radial clearance 2 groups. Non-standard clearance, in the case of special radial clearance and axial clearance, the relevant limit value should be expressed in μm after the letter R (radial clearance) or A (axial clearance), and the number Separate them with dots. Example: 6210.R10.20——6210 bearing, radial clearance 10 μm to 20 μm. 6212.A120.160 – 6212 bearings, axial clearance 120 μm to 160 μm. Subsequent code – bearing for testing noise F3 – low noise bearing. It mainly refers to cylindrical roller bearings and deep groove ball bearings with inner diameter d > 60mm or more. Example: 6213.F3 . G——Low noise bearing. It mainly refers to deep groove ball bearings with inner diameter d ≤ 60mm. Example: 6207.G suffix code
——Heat treatment S0——The bearing ring has been tempered at high temperature, and the working temperature can reach 150 ℃.
S1——The bearing ring has been tempered at high temperature, and the working temperature can reach 200 ℃. S2——The bearing ring has been tempered at high temperature, and the working temperature can reach 250 ℃. S3——The bearing ring has been tempered at high temperature, and the working temperature can reach 300 ℃. S4——The bearing ring has been tempered at high temperature, and the working temperature can reach 350 ℃. Subsequent code – special technical conditions F•• – continuous numbered manufacturing technical conditions. Example: F80——Bearing inner and outer diameter tolerance and radial clearance compression.
K••——Continuously numbered inspection technical conditions. Example K5——Bearing inner and outer diameter tolerance compression. .ZB——Cylindrical rollers with crowns over 80mm in diameter. Example: NU
364. ZB. .ZB2——The convexity at both ends of the needle roller is greater than the general technical requirements. Example: K18 × 26 × 20F .ZB2. ZW——double row needle roller and cage assembly. Example: K20 × 25 ×
40FZW. .700••• – consecutively numbered specifications starting with 700000. Z52JN.790144——The bearing can be used at high temperature and low speed. After special heat treatment, the cage is stamped and riveted with steel plate, with large clearance. After phosphating treatment, it is filled with grease. The service temperature can exceed 270 ℃. Subsequent code—special technical conditions KDA——Split inner ring/; Split inner ring K——Tapered bore 1:12 K30——Tapered bore 1:30 N——circular in the outer ring for snap ring S——Lubricating groove and bores in the outer ring The “S” suffix has been canceled in the new E1 series! Outer ring oil grooves and oil holes are now standard. W03B Stainless steel bearing N2 two retaining troves for fixing the outer ring The two retaining troves for fixing the outer ring are post-coded – paired bearings and machine tool spindle bearings 1) paired bearings that meet K technical conditions, the following special technologies Conditions related to paired bearings:
K1——Two sets of deep groove ball bearings are installed in pairs to bear one-way axial load. K2——Two sets of deep groove ball bearings are installed in pairs to bear bidirectional axial load. K3——Two sets of deep groove ball shafts are installed back to back without clearance (O type installation). K4——Two sets of deep groove ball bearings are installed face-to-face without clearance (X type installation). K6——Two sets of angular contact ball bearings are installed in pairs to bear one-way axial load. K7——Two sets of angular contact ball bearings are installed back-to-back without clearance (O-type installation). K8—Two sets of angular contact ball bearings are installed face to face without clearance (X type installation) K9—Two sets of tapered roller bearings with a spacer between the inner and outer rings are installed in pairs to bear unidirectional axial load. K10—Two sets of tapered roller bearings with a spacer between the inner and outer rings are installed back-to-back without clearance (O-type installation) K11—Two sets of tapered roller bearings with a spacer between the outer rings are mounted face-to-face without clearance installation (X-type installation). Bearings configured in pairs or groups need to be packaged together for delivery, or marked as belonging to a pair. Bearings of different groups are not interchangeable. When installing bearings belonging to the same group, the installation should be carried out according to the marks and positioning lines. If each pair of bearings is configured according to a certain amount of axial or radial clearance, the clearance should be marked according to item 1 and 2) of item (7) after the K technical condition. For example, 31314A .K11.A100.140 means two sets of 31314A single row tapered roller bearings, installed face to face, with a certain distance spacer between the outer rings, the axial clearance of the bearings before assembly is between 100 μm and 140 μm, and after assembly Gap is zero. Universal paired bearings can be installed in any pair (tandem, face-to-face or back-to-back), and the rear codes are UA, UO and UL. .UA – There is a small axial clearance when the bearings are installed face-to-face or back-to-back. .UO – No backlash when bearings are mounted face-to-face or back-to-back. .UL – Slight pre-interference when bearings are mounted face-to-face or back-to-back. For example, B 7004C .TPA.P4.K5.UL indicates an angular contact ball bearing with a contact angle of 15o for the main shaft, phenolic laminated cloth tube
FAG bearing model suffix English letters represent the specific meaning
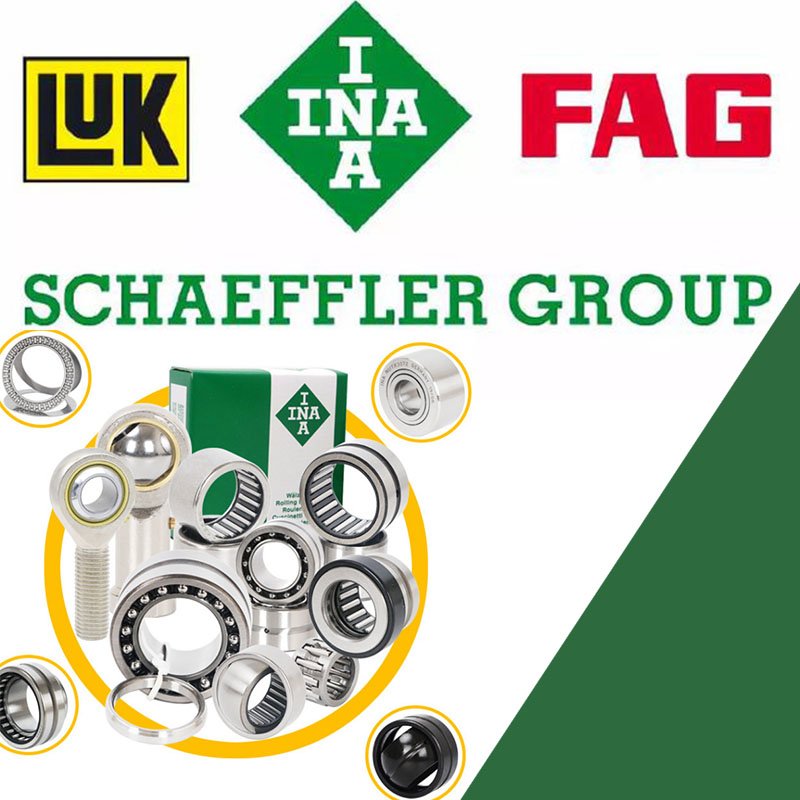
19
Feb